Revolutionizing Industries with Rubber Bellows Prototypes
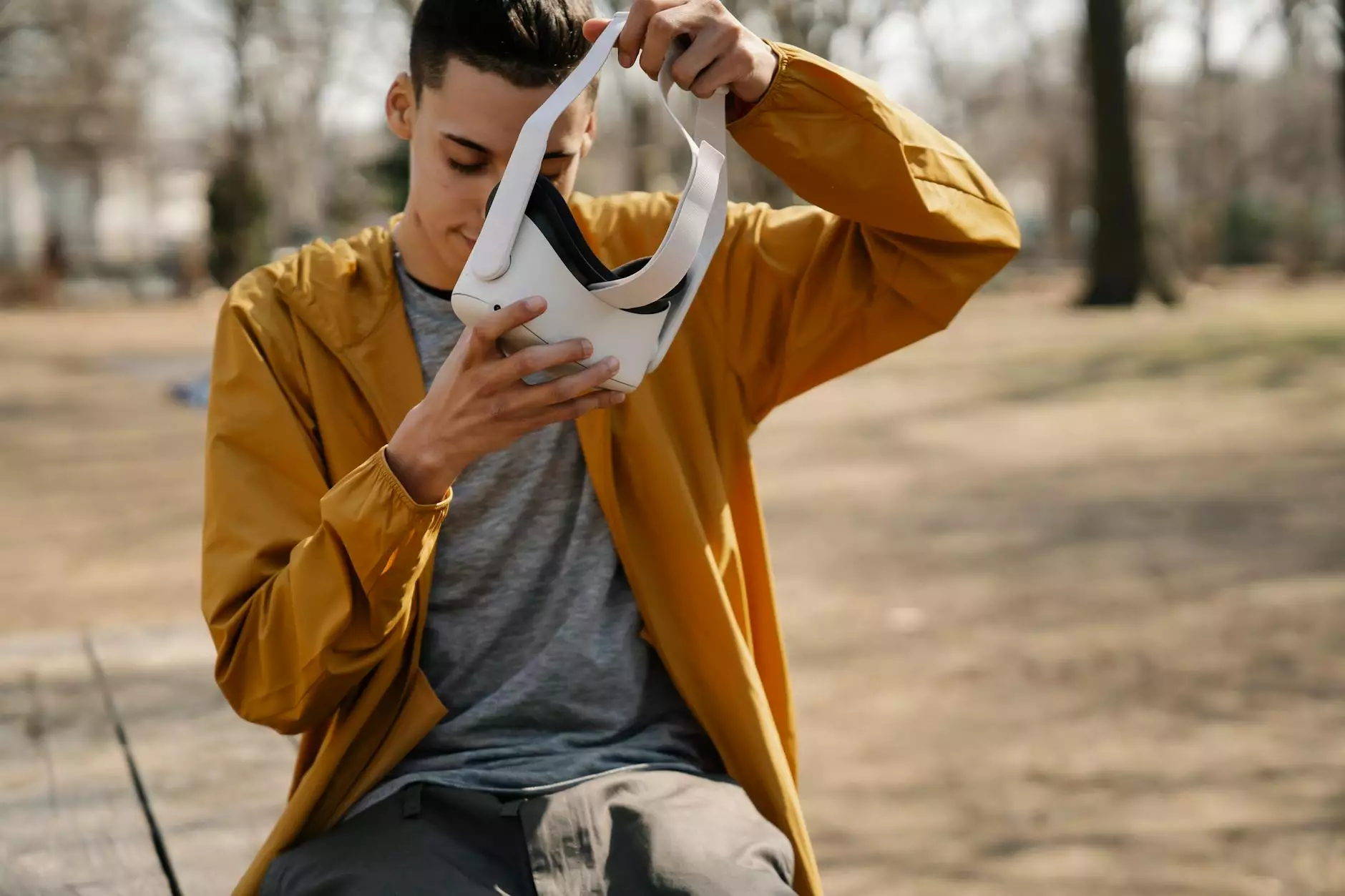
In today’s rapidly advancing technological environment, businesses are constantly seeking innovative solutions to enhance their product offerings. One such innovation is the rubber bellows prototype, a versatile and crucial component in a myriad of applications across various industries. In this article, we will explore the benefits, applications, and design considerations related to rubber bellows prototypes, highlighting the vital role they play in modern business solutions.
The Essence of Rubber Bellows Prototypes
Rubber bellows are flexible protective coverings designed to absorb movement and accommodate motion without compromising the integrity of the machinery or the components they shield. A prototype is an essential precursor to the final product, allowing for testing and refinement of design concepts. For businesses like O Victor Group, specializing in accessories and 3D printing, the development of high-quality rubber bellows prototypes is imperative for achieving superior product performance and reliability.
Why Choose Rubber for Bellows Prototypes?
When it comes to selecting materials for bellows prototypes, rubber stands out due to its unique properties. Here are several reasons why rubber is the preferred material:
- Flexibility: Rubber bellows can expand and contract, making them ideal for applications where movement is inherent.
- Durability: Rubber exhibits excellent resistance to wear, tear, and harsh environmental conditions, ensuring a longer lifespan.
- Sealing Properties: Rubber effectively seals against contaminants, preventing dust and moisture from entering sensitive areas.
- Cost-Effectiveness: Producing rubber bellows prototypes is generally more cost-effective compared to other materials, making them suitable for businesses looking to optimize their budgets.
The Role of 3D Printing in Rubber Bellows Prototyping
3D printing technology has transformed the manufacturing landscape, especially in the prototyping phase. Businesses like O Victor Group leverage 3D printing to create precise and custom rubber bellows prototypes more efficiently than traditional manufacturing methods.
Benefits of 3D Printing Rubber Bellows Prototypes
- Rapid Prototyping: 3D printing allows for quicker design iterations, enabling businesses to refine their products efficiently.
- Customization: Each prototype can be tailored to specific requirements, ensuring the final product meets precise industry standards.
- Material Savings: With 3D printing, businesses can minimize waste by using just the right amount of material needed for each prototype.
- Complex Geometries: Complex designs that were once hard to achieve can now be realized with ease through advanced 3D printing techniques.
Applications of Rubber Bellows Prototypes Across Industries
Rubber bellows prototypes have a vast range of applications across various sectors. Here are some predominant industries where these prototypes are utilized:
1. Automotive Industry
The automotive sector frequently employs rubber bellows to protect sensitive components from dirt, moisture, and physical damage. Common applications include:
- CV Joints: Safeguarding the joint assemblies from contaminants.
- Steering Assemblies: Ensuring smooth operation while protecting the steering components.
2. Aerospace Industry
In aerospace applications, rubber bellows prototypes are integrated into systems for vibration isolation and as seals in hydraulic systems. Their resilience in extreme conditions enhances the reliability and safety of aircraft.
3. Robotics and Automation
In the realm of robotics, rubber bellows play a critical role in protecting actuators and joints from dust and debris. This ensures longevity and consistent performance of robotic systems.
4. Marine Applications
Marine vessels often utilize rubber bellows to protect portholes and machinery from water ingress, where durability and flexibility are paramount.
Design Considerations for Rubber Bellows Prototypes
Creating effective rubber bellows prototypes requires thoughtful design considerations. Below are some critical factors to consider:
- Dimensions: Accurate measurements are essential to ensure proper fit and function in the intended application.
- Material Selection: Choose rubber composites that align with the environmental challenges the prototype will face.
- Movement Requirements: Understand the specific motion requirements—compression, extension, or torsion—and design accordingly.
- Manufacturing Capabilities: Ensure that your design takes into account the limitations and capabilities of the chosen manufacturing process.
Innovations in Rubber Bellows Prototypes
As technology progresses, so does the evolution of rubber bellows prototypes. Innovative advancements such as the integration of smart materials and sensors allow rubber bellows to proactively respond to changes in shape or environmental conditions, significantly enhancing their functionality across applications.
Smart Rubber Bellows
Integrating sensors within rubber bellows can potentially monitor stretch, environmental temperature, and other vital performance metrics. This transformation leads to more intelligent systems, minimizing maintenance needs and enhancing performance reliability.
The Future of Rubber Bellows Prototypes
Looking ahead, the trajectory for rubber bellows prototypes is promising. With emerging technologies such as AI-driven design algorithms and advanced materials science, the efficacy and applications of rubber bellows are set to expand further. Companies investing in these technologies, such as O Victor Group, are poised to lead the market with innovative solutions catered to an evolving industrial landscape.
Conclusion
The use of rubber bellows prototypes represents a critical aspect of modern manufacturing and product design, offering unmatched versatility and functionality. As industries continue to evolve, embracing innovations such as 3D printing and intelligent materials will be vital for staying competitive. For businesses like O Victor Group, focusing on creating high-quality rubber bellows prototypes will ensure success in meeting customer demands while driving forward the industry standards.
Investing in quality and innovation not only enhances product durability and performance but also fosters growth and sustainability within the industry. Whether you are in automotive, aerospace, or robotics, understanding the role of rubber bellows prototypes can significantly improve your business outcomes.