Understanding Industrial Vacuum System Design
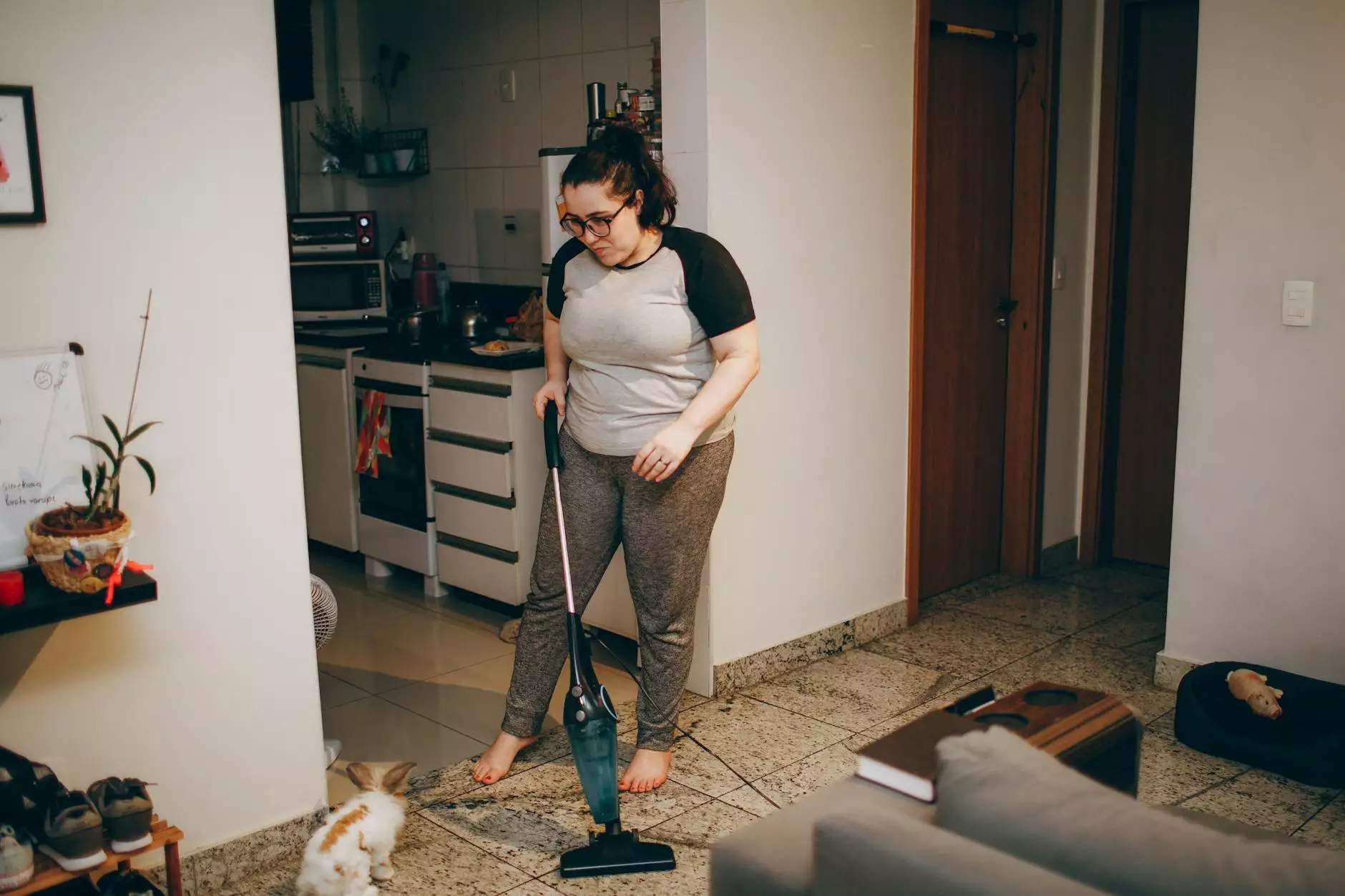
In the realm of industrial operations, industrial vacuum system design plays a crucial role in enhancing efficiency and safety. This article delves deep into the various aspects of industrial vacuum systems, covering their design, functionality, applications, and how to optimize them for better performance.
The Importance of Industrial Vacuum Systems
Vacuum systems are essential in numerous industrial applications, providing solutions for material handling, dust control, and process improvement. Here are some key benefits:
- Enhanced Efficiency: By removing debris and contaminants, vacuum systems streamline production processes.
- Improved Safety: Effective dust collection reduces workplace hazards, ensuring a safer working environment.
- Cost Savings: Well-designed systems can save significant costs on cleaning and maintenance.
Components of an Industrial Vacuum System
An industrial vacuum system comprises various components, each playing a vital role in its overall functionality:
1. Vacuum Producer
The heart of any vacuum system, the vacuum producer, creates the suction necessary to move materials. There are several types:
- Positive Displacement Pumps: Efficient for heavy materials.
- Centrifugal Pumps: Ideal for lighter materials and large air volumes.
- Blower Systems: Useful for general applications where a constant flow is required.
2. Filtration Systems
Filtration is critical in maintaining air quality and ensuring machinery protection. Some common filters include:
- HEPA Filters: Effective in trapping fine particles.
- Bag Filters: Cost-effective for general dust collection.
- Cyclone Separators: Useful for removing larger particles before they reach the main filter.
3. Collection Systems
Once materials are vacuumed, they need to be collected efficiently. Options include:
- Storage Drums: Ideal for high-capacity systems.
- Totes: Versatile for various materials.
- Pneumatic Conveying Systems: Automated solutions for transporting materials over distances.
Key Considerations in Industrial Vacuum System Design
Designing an effective industrial vacuum system requires careful consideration of several factors:
1. Application Requirements
Every industry has unique needs. For instance, a food processing plant's vacuum system would differ significantly from one in a pharmaceutical setting. Understanding your application's specific requirements is vital in determining:
- The type of materials being handled
- The required suction power
- The environment (e.g., explosion risks, temperature conditions)
2. System Scalability
As businesses grow, so do their operational needs. It's essential to design vacuum systems with scalability in mind, allowing easy expansion or modification without significant restructuring.
3. Energy Efficiency
In an era of increasing energy costs, designing a vacuum system that maximizes efficiency is crucial. Consider components that offer optimal power consumption:
- Variable Speed Drives: Allow for regulated power based on current needs.
- Efficient Motors: Reduced energy consumption while maintaining performance.
Applications of Industrial Vacuum Systems
Industrial vacuum systems are versatile, finding applications across various sectors, including:
1. Manufacturing
In manufacturing environments, vacuum systems aid in handling bulk materials, removing debris, and enhancing overall production efficiency.
2. Food Processing
In food processing, maintaining hygiene is paramount. Vacuum systems help in preventing cross-contamination and ensuring a clean workspace.
3. Pharmaceuticals
For pharmaceutical manufacturers, the vacuum system is essential in maintaining sterile environments and adhering to stringent regulatory compliance.
4. Chemical Processing
In chemical plants, industrial vacuum systems are used to safely handle volatile materials and ensure the integrity of processes.
Designing a Custom Industrial Vacuum System
Custom design is key when it comes to industrial vacuum system design. To develop a system that meets specific operational needs, follow these steps:
1. Assess Your Needs
Conduct a thorough analysis of your processes. What materials do you need to handle? What are the volume requirements? This step is critical for accurate design.
2. Engage Experts
Involving experts during the design phase will ensure you benefit from specialized knowledge that takes into account the latest technologies and best practices.
3. Prototype and Test
Create a prototype of your vacuum system and run tests to ensure it meets operational expectations. This phase helps identify potential issues before full-scale implementation.
Maintaining Your Industrial Vacuum System
Once your system is installed, proper maintenance is essential for longevity and efficiency:
1. Regular Inspections
Schedule ongoing inspections to identify wear and tear, ensuring components are functioning correctly.
2. Filter Maintenance
Filters should be checked and replaced regularly to maintain optimal air flow and filtration efficiency.
3. System Cleaning
Regular cleaning of the vacuum system components prevents build-up and ensures continued high performance.
Conclusion
Investing in an industrial vacuum system design is not just a matter of improving workflow; it’s about enhancing safety, efficiency, and cost-effectiveness. By understanding the components, benefits, applications, and maintenance of these systems, you can make informed decisions that impact your industrial operations positively. Integrating best practices into your design and maintenance schedules will ensure that your vacuum systems serve your business for years to come.
For businesses looking to enhance their operations, tmm.com.tr offers a wealth of resources and solutions to assist in the effective implementation and management of industrial vacuum systems.