Electric Injection: Revolutionizing Metal Fabrication
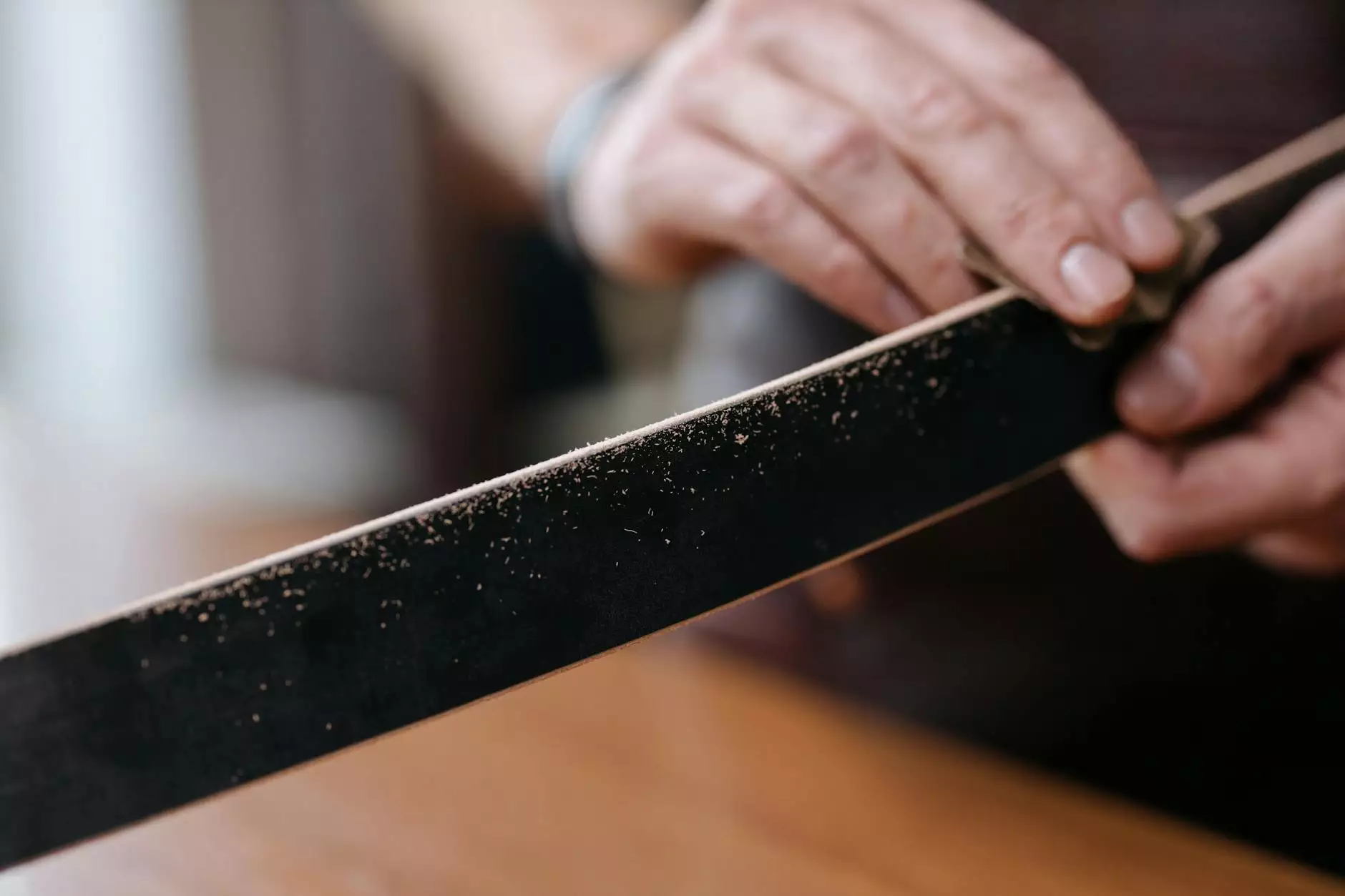
Electric injection is not merely a technical term; it embodies a revolutionary approach reshaping the landscape of the manufacturing industry, particularly in the field of metal fabrication. As industries evolve, so do the processes that define them. Electric injection harnesses cutting-edge technology to enhance productivity, precision, and sustainability in metal fabrication processes, ensuring businesses can meet the demands of a rapidly changing market.
The Concept of Electric Injection
At its core, electric injection refers to the process through which molten materials are injected into a mold using electrical mechanisms. This innovative technique offers numerous advantages over traditional methods, primarily through the enhanced control and efficiency it provides. By utilizing electric power, manufacturers can achieve a level of precision that was previously unattainable, leading to superior product quality and reduced wastage.
Benefits of Electric Injection in Metal Fabrication
Adopting electric injection technology in metal fabrication comes with an array of compelling benefits:
- Improved Precision: Electric injection allows for precise control of the injection process, resulting in intricate designs and minimal tolerances.
- Increased Efficiency: Faster cycle times reduce the time required for production, enhancing overall operational efficiency.
- Cost-Effectiveness: Despite the initial investment, the ongoing savings in material usage and energy efficiency quickly offset costs.
- Environmental Sustainability: Electric injection reduces carbon emissions associated with traditional fuel-based machinery, contributing to greener practices.
- Versatility: This technology accommodates a wide range of materials, expanding design possibilities for manufacturers.
Applications of Electric Injection
The applications of electric injection in the realm of metal fabrication are extensive and varied:
1. Automotive Industry
In the automotive sector, electric injection is employed to manufacture components such as engine blocks, transmission housings, and intricate interior fittings. The precision and efficiency of electric injection processes allow for the production of lightweight yet durable parts that contribute to enhanced vehicle performance.
2. Aerospace Engineering
Aerospace applications require components with superior strength-to-weight ratios. Electric injection technology enables the creation of complex shapes that adhere to the strict standards for safety and performance inherent in the aerospace industry.
3. Electronics
As electronics continue to miniaturize, the need for precision components increases. Electric injection is valuable for producing intricate enclosures, connectors, and circuit boards that support the demanding specifications of modern electronics.
4. Medical Devices
Electric injection is a game-changer in the medical field, facilitating the manufacture of biologically compatible devices, surgical instruments, and patient monitoring equipment, where precision and reliability are paramount.
Challenges and Considerations
While the benefits of electric injection are considerable, there are challenges that manufacturers must address. These include:
- Initial Investment: The cost of acquiring electric injection machinery can be high, which may deter some manufacturers from adopting the technology.
- Training Requirements: Employees must be trained to operate advanced electric injection systems efficiently, which can incur additional costs and time investments.
- Technology Adaptability: Some existing production lines may require significant modifications to integrate electric injection technology seamlessly.
Future Trends in Electric Injection Technology
The future of metal fabrication lies in innovation. As electric injection technology continues to advance, several trends are emerging that will further shape its role in manufacturing:
1. Smart Manufacturing
With the rise of the Internet of Things (IoT), smart manufacturing is becoming increasingly common. Electric injection systems integrated with IoT technologies will permit real-time monitoring and adjustments, optimizing production processes further.
2. Hybrid Technologies
Combining electric injection with other technologies like 3D printing could lead to novel fabrication methods. These hybrid techniques may enable the production of more complex components that meet the unique requirements of various industries.
3. Enhanced Material Options
Research is ongoing into new alloys and materials specifically designed for electric injection processes. This could open new avenues in terms of product capabilities and performance.
How Deepmould.net is Leading the Charge
As a distinguished player in the metal fabrication domain, Deepmould.net is committed to embracing cutting-edge technologies like electric injection. Our dedication to innovation ensures that we remain at the forefront of industry advancements, providing our clients with superior products and services.
With a focus on detail and quality, we combine advanced electric injection technologies with skilled craftsmanship to deliver unparalleled results. Our experienced team is continually exploring ways to leverage this technology to enhance not only our operations but also the solutions we offer to our clients.
Conclusion: The Imperative for Electric Injection in Modern Manufacturing
Embracing electric injection technology is no longer optional for businesses looking to thrive in today's competitive market. The transition to this innovative manufacturing process represents a significant leap toward sustainability, efficiency, and precision. As the demand for high-quality metal products increases, companies that incorporate electric injection into their fabrication processes will undoubtedly have a competitive advantage.
By investing in electric injection technology and partnering with forward-thinking companies like Deepmould.net, businesses can ensure they are well-positioned for future growth and success. The future of metal fabrication is bright, and electric injection will undoubtedly play a pivotal role in shaping that future.