Maximizing Innovation with Rapid CNC Prototyping in Metal Fabrication & Manufacturing
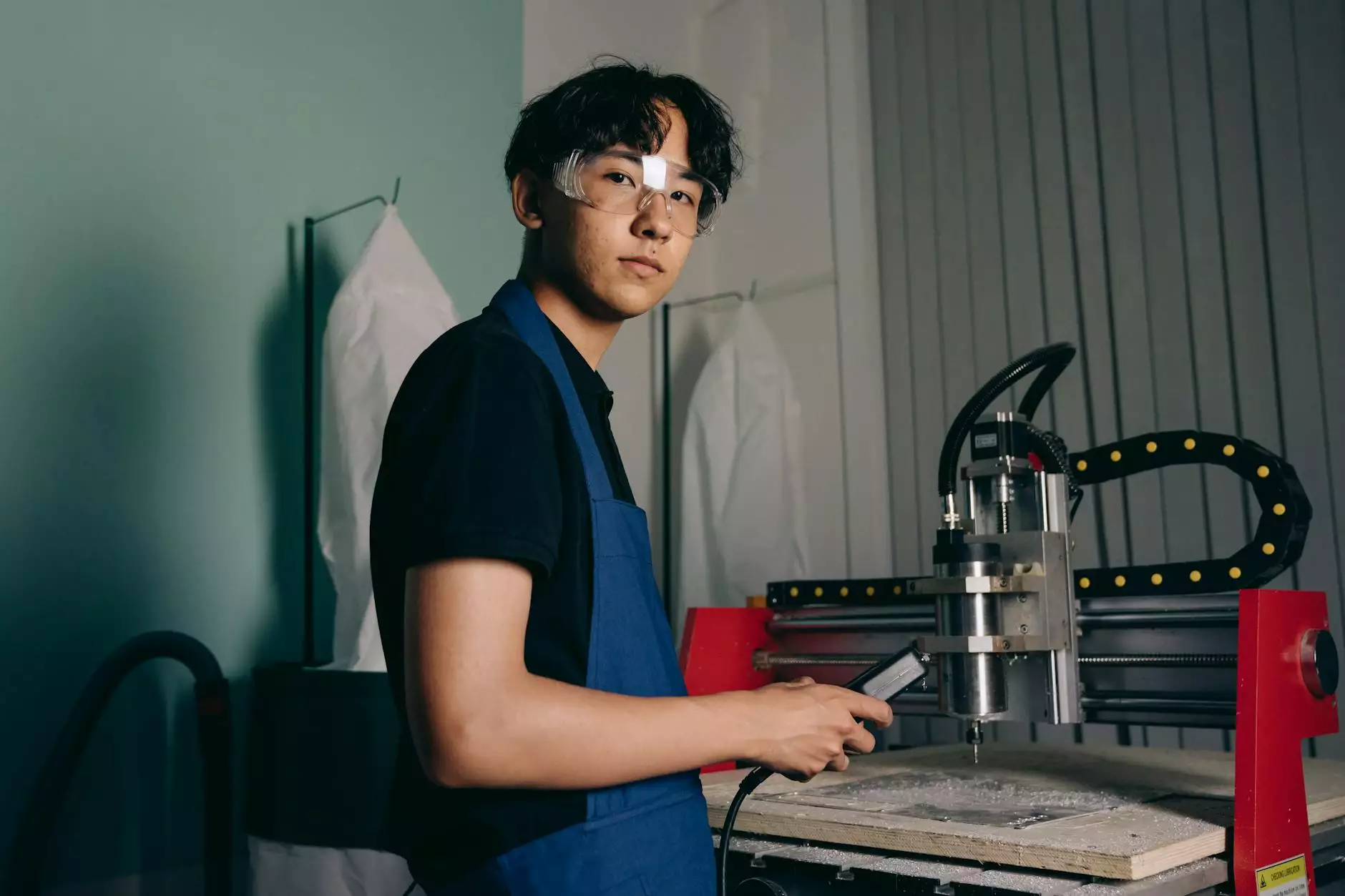
In the fiercely competitive landscape of modern manufacturing, the ability to rapidly develop, test, and refine product designs can be the key differentiator that propels a business to industry leadership. At the forefront of this technological revolution is rapid CNC prototyping, an essential process that accelerates product development cycles, improves accuracy, and significantly reduces costs. Companies like deepmould.net, specializing in Metal Fabricators, exemplify how integrating rapid CNC prototyping can transform traditional manufacturing into a more agile, innovative, and customer-centric operation.
Understanding Rapid CNC Prototyping: A Game-Changer in Metal Fabrication
Rapid CNC prototyping refers to the use of computer-controlled machining processes to quickly produce functional prototypes, parts, or components directly from CAD models. Unlike traditional manufacturing, which often involves lengthy setup times and tooling production, rapid CNC prototyping streamlines the journey from design to physical product. This method offers unparalleled precision, flexibility, and speed, making it indispensable for industries demanding fast-paced innovation and high-quality outputs.
Key Features of Rapid CNC Prototyping
- Speed: Accelerates prototype development from weeks to days or even hours.
- Precision: Ensures dimensional accuracy and surface finish suitable for functional testing.
- Flexibility: Capable of working with various metals such as aluminum, stainless steel, titanium, and more.
- Cost-Effective: Reduces tooling costs and material waste compared to traditional methods.
- Design Verification: Provides a tangible representation to identify potential issues early.
Benefits of Incorporating Rapid CNC Prototyping in Metal Fabrication
The integration of rapid CNC prototyping into metal fabrication processes presents a multitude of advantages that empower manufacturers to stay ahead in a highly competitive marketplace:
1. Accelerated Product Development Cycles
Traditional prototyping methods can delay product launches by extending development timelines. Using rapid CNC prototyping, businesses can drastically cut down these durations, enabling faster iteration, testing, and refinement. This agility allows companies to respond swiftly to market trends and customer demands.
2. Enhanced Design Accuracy and Functionality Testing
Prototypes produced via rapid CNC prototyping accurately replicate final production parts, including complex geometries and fine details. This precision facilitates comprehensive testing of fit, form, and function, reducing the risk of costly redesigns post-production.
3. Cost Optimization and Waste Reduction
The reduced need for expensive molds and tooling, along with the precise material deposition capabilities of CNC machines, minimizes waste and material costs. This efficiency is particularly significant when developing high-value metals like titanium or specialty alloys.
4. Fostering Innovation and Design Flexibility
With rapid CNC prototyping, designers can experiment with complex structures, intricate internal channels, and optimized shapes that traditional methods might struggle to produce quickly. This freedom fosters innovation and allows for bespoke solutions tailored to specific applications.
5. Quality Assurance and Risk Mitigation
Producing prototypes early in the development process allows manufacturers to identify and rectify issues before mass production, ultimately ensuring higher quality final products and reducing costly recalls or redesigns.
The Role of Deepmould.net and Metal Fabricators in the Future of Rapid CNC Prototyping
As industry leaders in metal fabrication, deepmould.net leverages cutting-edge rapid CNC prototyping technologies to deliver unparalleled precision and reliability. Their expertise covers a wide array of metals and complex machining techniques, ensuring that clients receive prototypes that meet exact specifications and quality standards. This approach significantly shortens product development timelines and boosts overall innovation output.
Why Choose Deep Mould for Rapid CNC Prototyping?
- State-of-the-Art Equipment: Advanced CNC machines capable of working with diverse metals and alloys.
- Expertise in Complex Machining: Skilled technicians capable of handling intricate designs and tight tolerances.
- Full-Service Support: From CAD/CAM integration to finishing and surface treatment, comprehensive solutions are provided.
- Fast Turnaround Times: Emphasizing efficiency without compromising quality to meet demanding deadlines.
- Cost-Effective Solutions: Optimizing processes to deliver high-quality prototypes at competitive prices.
The Process of Rapid CNC Prototyping in Metal Manufacturing
The process begins with detailed CAD designs that are meticulously prepared for manufacturing via CAM software. These files are then imported into high-precision CNC machines, which precisely cut, mill, or turn the metal blocks into the desired prototype parts. The entire workflow is optimized to ensure quick turnaround times, allowing for rapid iterations and modifications.
Essential Steps in the Rapid CNC Prototyping Workflow
- Design Preparation: Creating detailed CAD models, verifying tolerances, and optimizing for machining.
- CAM Programming: Converting CAD into machine instructions, toolpath generation, and process simulation.
- Material Selection: Choosing the appropriate metal based on application, strength, and finishing requirements.
- Machining: Precision milling, turning, or drilling on CNC equipment with real-time quality monitoring.
- Finishing: Surface treatments, polishing, and quality inspections to ensure adherence to specifications.
- Testing and Evaluation: Conducting functional tests, fit checks, and modifications if necessary.
Advancing the Future of Manufacturing with Rapid CNC Prototyping
The ongoing evolution of rapid CNC prototyping technology promises even greater capabilities, including faster processing speeds, more complex material options, and integration with digital manufacturing ecosystems. These advancements will enable manufacturers to develop innovative products more quickly, reduce time-to-market, and maintain a competitive edge.
Industries such as aerospace, automotive, medical devices, and consumer electronics are increasingly adopting these technologies to streamline their development pipelines. As trusted partners like deepmould.net continue to push the boundaries of what is possible, the future of metal fabrication is poised for remarkable growth and innovation.
Conclusion: Embracing Rapid CNC Prototyping for Competitive Advantage
In summary, rapid CNC prototyping is an indispensable tool that empowers manufacturers to rapidly transform digital designs into tangible, high-quality metal prototypes. Its ability to deliver precision, speed, and cost savings makes it a cornerstone of modern metal fabrication. Businesses that leverage this technology, especially those partnering with expert providers like deepmould.net, position themselves for accelerated innovation, reduced development costs, and unmatched market responsiveness.
As the manufacturing landscape continues to evolve, staying at the forefront of rapid CNC prototyping and related technologies will be essential for companies aiming to lead in their industries. Embracing these advancements today ensures sustainability, growth, and long-term success well into the future.